Material Smear and Its Removal
Material smearing can have a very detrimental effect on an LPI inspection as defects that are normally open to the surface can be partially or completely covered over. Some of the processes that can cause material to smear include machining, honing, lapping, sanding, scraping, grit blasting, tumble de burring, and peening operations. When high pressure is used, some cleaning operations, such as vapor and steam cleaning, can also cause material to smear in the softer materials. Softer materials, such as plastics and aluminum alloys, are most prone to smearing but many other materials, such as steel, titanium and Inconel alloys, have also been shown to smear. To evaluate the effect of a process on liquid penetrant inspection, cracked specimens are typically inspected before and after performing the potential smearing operation and a comparison between the inspection results are made. It must be noted that under carefully controlled conditions, material smear can be avoided. Whenever parts have been mechanically processed prior to LPI, an evaluation should be performed to determine if flaw detectability has been compromised. If material smearing is a problem, an etching process can be used to remove the smeared material prior to inspection. The curves below illustrate the effect that metal smearing can have on the probability of detection for a defect and how etching the sample surface improves detectability.
The top curve shows the probability of detecting a crack versus crack length for as-machined aluminum specimens. The bottom curve shows the POD for the same aluminum specimens after their surfaces had been etched. Comparing the crack lengths where the curves reach a POD level of 90%, it can be seen that in the as-machined condition, the crack length would need to be 0.4 inches long. However, when the surface is etched, cracks under 0.10 inch can be detected with a 90 % probability.
Removal of Material Smearing
Etching of the specimens can return the flaw to the pre-mechanical processing level of detectability. The amount of material that must be removed by the etching process depends on the amount of material that has been smeared and should be determined experimentally. Volume two of the Nondestructive Testing Handbook provides a great deal of information on material smearing and the amount of etching required to remove a smeared metal. The handbook includes a number of photographs such as the set below that graphically show the effects of metal smearing.
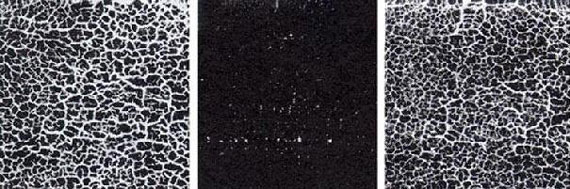
When an etchant is used, it must be properly removed from the part before applying penetrant. Experts in the penetrant field warn that acid and caustic entrapment from a prepenetrant etch can have disastrous effects on the penetrant inspection. Careful cleaning of both acid and caustic etches before penetrant inspection is highly recommended. There are several other risks to the parts being processed when an etchant is used. First, since the etching process is removing metal from the surface of the part, the minimum dimensional tolerances of the part must be considered. A second possible risk is that the etching process could have an effect on the material properties of the part. The chemical etchant used should uniformly remove material from the surface and should not etch microstructural features (such as grain boundaries) preferentially. Ideally, a study should be conducted to evaluate the effects of the etching process (or other chemical process) on the mechanical properties and performance of the component.
References:
Rummel, W.D. and Matzkanin, G. A., Nondestructive Evaluation (NDE) Capabilities Data Book, Published by the Nondestructive Testing Information Analysis Center (NTIAC), NTIAC #DB-95-02, May 1996.
Nondestructive Testing Handbook, Vol. 2, Liquid Penetrant Tests, Robert McMaster, et al., American Society for Nondestructive Testing, 1982.